Synergy
ACRO
1570mm EPP
Crash Resistant Trainer / Sports Aerobatic Slope Soarer
Designed
by Stan Yeo
Produced
by PHOENIX MODEL PRODUCTS
Introduction
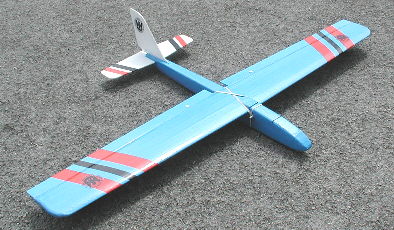
The Synergy
Acro is a stylish advanced sports aerobatic EPP model capable of virtually
all aerobatic manoeuvres that a model glider can perform. In fact it's
aerobatic repertoire is more limited by the imagination of the pilot and
the prevailing conditions than by the model itself, particularly if flapperons
and coupled flap elevator is used. Building time should be about ¼ to
1/3 that of an equivalent wood and foam construction model, i.e. 15 -
20 hours.
Before starting
please read these instructions in conjunction with the full size plan
and familiarise yourself with the parts. If you do require assistance
please do not hesitate to contact us.
Tools
/ Materials Required
The glues
required are thin Superglue, (used for wood joints), 2 part epoxy (12
minute recommended) used for wing spars and braces. Spray impact adhesive,
used to glue EPP and prime foam prior to covering. Also required is an
external covering to go over the top of the base covering material, which
is cross weave filament tape (CW Tape) to decorate the model and stop
the ultra violet light damaging the CW tape. This can be a coloured vinyl
sticky back tape (recommended) or an iron film. Tools required consist
of a soldering iron and multi-core solder, a modelling knife, sanding
block and a pair of pliers. A long (75mm) bladed knife made from a hacksaw
blade is also very useful. 10mm thick Sundela board is recommended for
use as a building board, small fitters square or set square, lead sheet,
masking tape, cling film plus a selection of long elastic bands.
R/C
Equipment
As a basic
three channel model the Synergy Acro requires 2 standard size servos for
the rudder and elevator controls plus 2 metal geared micro
servos (Hitec HS81MG recommended) for the ailerons, a 4 channel receiver
and a square receiver battery pack. Please do not attempt to use plastic
geared micros as in all probability a heavy landing will strip the gears
and replacing them will cancel out any money saved; besides it could also
spoil a good days flying! For flapperons and coupled flap / elevator a
6 channel receiver is required i.e. the GWS 8 channel micro Rx.
Building
the Fuselage
- Lightly sand ply fuselage side to remove splinters and release agent.
- Drill wing dowel holes in ply sides. Ensure a tight fit.
- Fit balsa
strip longerons to ply sides using Superglue leaving gaps for balsa
blocks. Check there is a left and right side !!
- Cover
plan with cling film and position fuselage sides above plan view of
fuselage, using wing dowels to assist with alignment. Position balsa
blocks. In conjunction with wing dowels use rubber bands stretched over
top of fuselage to position sides correctly. Use set square for final
vertical alignment.
- Fit balsa
block at front and rear of wing, plus block at fuselage
bottom
under wing trailing edge (TE). DO NOT GLUE DOWELS.
- Fit nose
former and join fuselage at tail. Fit ply tail seat.
- Fit ply
fuselage bottom forward of wing TE and ply top at nose, forward of hatch.
- Spray
with impact adhesive, one side of fuselage and one EPP foam side and
allow a couple of minutes for solvent to evaporate. Fit foam side to
fuselage ensuring that the 'spare' is at the nose end (required to form
cavity for nose weight).
- Using
sharp long bladed knife trim EPP foam ensuring that it is cut square
to fuselage top and bottom.
- Fit other
EPP fuselage side and trim as before.
- Decide
which side of the servo the control rods need to be connected for the
controls to operate in correct sense. Remember control exit is on opposite
side. Insert piano wire push rod into control outer and fit elevator
control rod checking that pushrod moves freely. Anchor to fuselage sides
in between wing TE and tailplane using balsa strip off-cuts or CW tape.
- Fit fuselage
bottom again ensuring any surplus is at nose end.
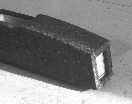
- Fit EPP
to nose top forward of hatch aligning with ends of EPP sides.
- Cut sheet
lead into 3 or 4, 30 mm sq. blocks and glue to front of nose former
inside EPP foam cavity.
- Fit noseblock
and trim any surplus.
- Remove
1.5mm strip of plastic from Correx Tailplane and Fin along hinge line
to form hinge (as shown on plan).
- Fit, (using
superglue) 10 mm triangular strip to base of Fin to line up with tailplane
as shown on plan. Check using set square that fin is square when resting
on base. Adjust as necessary.
- Mark tailplane
centre on Correx and glue Fin in position using Superglue ensuring it
is square with the Tailplane. TIP If fin is not vertical after gluing
to tailplane, cut balsa strip along its length on inside of lean and
insert sliver of thin card to correct lean. When satisfied fix with
Superglue.
- Cut fuselage
top to shape above tailplane seat and relieve inside of
fin
slot to accommodate 10 mm triangular strip at Fin base.
- Epoxy
Tailplane to Fuselage ensuring that it is both square and in line with
the axis of the fuselage i.e. Fin has not got built in left or right
rudder.
- Position
fuselage top hot wire 'drill' hole for Rudder control rod (use non -
Z bend end of push rod). Only heat the last 10 mm. Drill a test hole
in scrap EPP - you will be surprised at how easy the foam melts!
- Fit rudder
control rod and check for freedom of movement as before.
- Fit fuselage
top. Trim to size as before and radius all corners using a sharp knife
and 'carving' action before final finishing with 180 grade wet & dry.
- Manufacture
hatch.
Building
the Wings.
- Using epoxy assemble main spar on flat surface as per plan and mark
centre line and spar top (determined by dihedral as a result of spar
tapes)
- Epoxy
rear spars to wing TE sections using masking tape to hold in place.
- Epoxy
one half of wing to main spar. Use a combination of masking tape and
not too tight rubber bands to hold EPP in place whilst epoxy sets. Take
great care to ensure that wing is properly seated against main spar
and equally positioned along it top and bottom. Smooth / remove any
surplus epoxy.
- Fit TE
spar brace. Note this will not be a perfect fit due to wing taper.
- Cut out
recesses in wing for aileron servo(s). All servos are fitted
behind
main spar. For twin aileron servo installation, lay wing upside down
on flat surface. Position servo behind main spar, stretch servo lead
in towards wing joint. Position servo so that the end of the lead extends
30 mm beyond wing join and cut 'snug' rectangular section out of wing
to accommodate servo. A long bladed scalpel is required for this operation.
Cut small slots for servo lugs and servo lead. Position servo in wing.
Turn wing right way up and slice top off 'rectangular' block to fill
cavity above the servo. Remove servo and glue insert in position. Repeat
for second servo.
- Shape
leading edge of ailerons according to wing servo installation (see plan).
- Check
length of ailerons, adjust as necessary. Shape tips (ailerons & wing)
Covering
Wing
- Before starting covering remove any dust that has collected in the
foam pores with a vacuum cleaner.
- Lightly
spray (nozzle 60mm from work) the wing with impact adhesive and allow
a couple of minutes for the solvent to evaporate.
- Lay a
strip of CW tape along edge of trailing edge such that the overlap is
equally spaced between top and bottom surface. Allow tape to overlap
wing joint each side by 50 - 60 mm.
- Apply
the next layer of tape on underside, of one wing panel, again overlapping
the wing joint by 50 - 60 mm. Allow for wing taper by overlapping first
strip at root by 5 mm and abutting rear spar at tip. Repeat for opposite
wing panel.
- Repeat
Step 4 for top surface of wing.
- Repeat
Steps 4 & 5 until wing is covered. Where there is loose tape around
compound curves slice tape to allow it to overlap. The technique for
leading edge is similar to that of fuselage corners, i.e. hold tape
at right angles to wing surface and run long bladed knife along tape
using opposite surface as a cutting guide. Lubricate knife blade with
White Spirit.
Fuselage
- Check fit of wing to fuselage and wing alignment with tailplane. Adjust
as necessary.
- Remove
control push rod if fitted and block ends of tubes to prevent ingress
of spray adhesive.
- Spray
fuselage with impact adhesive. Allow 2 or 3 minutes for solvent to evaporate.
- Start
taping fuselage by laying first strip of CW tape full length of fuselage
in line with underside of tailplane. Repeat for opposite side. Lay second
strip alongside with an overlap of 8 - 10 mm. Trim, using long bladed
knife lubricated with white spirit, by using fuselage bottom as a guide
for the knife blade and using free hand to keep tension on tape whilst
cutting. It may be necessary to place weight on fuselage during this
operation to stop it moving whilst trimming the CW tape.
- Repeat
above until fuselage is covered. Treat the Fin / Tailplane joint as
a separate item.
Final
Covering
It is recommended
that the top surface of the wing and the fuselage is covered in an opaque
material such as a coloured vinyl sticky back tape or iron on heat shrink
film such as Profilm or Easycoat. There are two reasons for this, one
to protect the base covering (CW tape) from the effects of Ultra Violet
light, the other simply for decoration. For this type of model we recommend
the vinyl tape as it is cheaper and is considerably quicker and easier
to apply. Remember a sports model's flying takes priority over looks.
Even so a more than creditable finish can be achieved with the coloured
vinyl tape.
If covering
with coloured vinyl tape, use a similar procedure to that of the CW tape.
On the rudder elevator wing, to prevent the tape lifting at the trailing
edge, overlap with Sellotape Diamond. Sellotape Diamond is also used to
seal the leading edge of the tailplane and fin to reduce drag. The coloured
vinyl tape we supply can be shrunk slightly with a cool iron if required
to remove small wrinkles. After covering fit wing dowels (use bent piece
of wire inserted in dowel holes from inside of fuselage to determine external
position) DO NOT GLUE DOWELS. Hinge ailerons using Sellotape Diamond.
Equipment
Installation
Rudder
Elevator Controls
After covering
installation of the radio equipment can be carried out
- Assemble Rudder & Elevator servos onto their balsa blocks. Do not
glue into place yet. Please note it will be necessary to offset the
rudder servo to allow use of a longer servo arm to achieve the required
rudder movement.
- Fit Rx battery in nose along with Rx and switch harness. Position
rudder and elevator servos in fuselage ensuring they do not foul wing
dowels or aileron servo (single servo installation).
- Check position of balance point. Adjust as necessary. This may require
repositioning of rudder elevator servos.
- When satisfied dribble Superglue down sides of servo mounting blocks
to secure. Use offcuts of 6 or 10 mm triangular strip at corners of
front and back of servo mounting blocks to provide added support.
- Remove servo arms from rudder & elevator servos. Zero trims on Tx.
Switch on R/C equipment and zero servos.
- Fit piano wire pushrods to servo arms (pushrod underneath servo arm)
and install pushrod/servo arm ensuring arm is as near to neutral as
possible. If using computerised Tx use Sub.Trim menu for final adjustment.
- Fit control horns and assemble snaplinks to threaded adapters. Check
depth of hole in threaded adaptor. With control surfaces in neutral
mark end of adapters on pushrods and allowing for depth of hole in adapter
cut pushrod to length.
- Remove snaplink assemble and using a pair of pliers, spring loaded
with a rubber band, tin the inside of threaded adapter hole. Do not
spend too long on this operation as you will melt snaplink!
- Replace snaplinks on control horn and with control surface in neutral
solder in place.
- Check controls for correct sense and range of movement. This may
entail connections the rudder pushroad to outer hole on servo arm and
inner hole on control horn to get maximum movement. It will probably
be the reverse for the elevators as less angular movement is required.
Aileron
Controls
- Cut away CW tape and install aileron servos.
- Cut slit along wing, each side, 1 mm wide, 3 mm deep to accommodate
servo leads. Bury servo leads in wing and cover slit with length of
25 mm wide CW tape.
- If using non-computerised transmitter (Tx) plug Y lead into aileron
channel in Rx and connect servos. Check ailerons are operating in correct
sense i.e. on application of Left aileron the left aileron moves UP.
Use servo reversing to correct if necessary.
- If using a computerised transmitter (Tx) plug aileron servo extension
leads into the aileron and flap channels on the Rx and connect servos.
Set transmitter up in Wing Flapperon mode and using Sub-Trim menu to
align aileron servo output arms (look along underside
of wing). Check for correct sense and adjust if necessary using Servo
Reversing facility. If no matter what you do one function is always
operating in the wrong sense swap the channels the servos are plugged
into. This should cure the problem.
- When satisfied servos are set up correctly CW tape in position.
- Make a female template of the mid-wing section and slide over wing.
This is used to set the ailerons to follow the line of the wing section.
- Manufacture aileron pushrods as per plan and fit. Adjust nylon clevis
as necessary to achieve neutral (see above)
Flying
- . Set the controls to give the following movements for initial flights:
- Rudder +/- 30 deg.
- Elevator +/- 12mm
- Ailerons +/- 15mm
- Flapperons (if fitted) +/- 6mm
- Adjust balance to within recommended limits. Prototypes required
50 - 80gms of lead in the nose. Check alignment of wing and tailplane
and wing to tailplane incidence (chord lines should be parallel). Laterally
balance wing and check that it is not twisted. If the wing is twisted,
twist back in the required direction and re-smooth covering tape in
position. If model is fitted with flapperons check zero flap is in fact
zero flap otherwise performance will be impaired! (see Prepare to Flap
article on website).
- The Synergy Acro is not a beginners model but if you lack the relevant
experience we suggest you get an experienced model flyer to test fly
your Acro for you. We also recommend you take out third party insurance.
This can be obtained through the British Model Flying Association (BMFA)
Tel No. 0116 2440028.
- Please remember all aerobatic manoeuvres require energy in the form
of speed to perform the manoeuvre. If the model has insufficient speed
it will fail to complete the manoeuvre or perform it half-heartedly.
Vertical or near vertical dives are not an efficient way to build up
speed. A 30 deg. dive is much more efficient. Avoid sudden control inputs.
In most cases all they do is scrub off speed and lose height. Try to
fly smoothly as not only do the manoeuvres look better but you will
be able to perform more of them before having to regain height. Try
stringing manoeuvres together i.e. do a stall turn and allow the model
to gain a little extra speed to do a loop or roll on the crosswind leg
before doing a stall turn in the opposite direction. Pay particular
attention to positioning and set yourself targets for each flying session.
- If the lift is good or you are having difficulty penetrating into
wind try taping ballast under the balance point. This will increase
penetration and help the model maintain speed through the manoeuvres.
- The suggested control settings are a starting point and can be adjusted
to suit your personal tastes. Adjust the balance point so that when
the model is trimmed the elevator is more or less in the neutral position.
On the fully aerobatic version confirmation that the balance point is
correct is usually indicated by how little down elevator is required
to maintain inverted level flight.
- Synergy Acro will take a lot of punishment. It is excellent for building
confidence and will add another dimension to your flying but please
remember if you take a big enough hammer to anything it will break.
The CW tape used for covering also degrades in ultra-violet light so
store the model in a relatively cool place away from direct sunlight.
- The Synergy Acro has a fully sym-metrical section so do not expect
it to stay up as well as an equivalent flat bottom section model in
light winds. It won't. This is why nearly all kit manufacturers avoid
using wings with fully symmetrical sections for aerobatic slope soarers.
We are almost unique in offering a selection of slope soarers with fully
symmetrical section wings without which the model, in our opinion, would
not be fully aerobatic and able to do some of the manoeuvres it can.
- Finally should you require further assistance or advice please contact
us either by letter, telephone, email or visit our website (http://www.phoenixmp.com)
where you will find a number of useful articles on various aspect of
model flying.
Happy flying
Stan Yeo
Synergy
021004
|